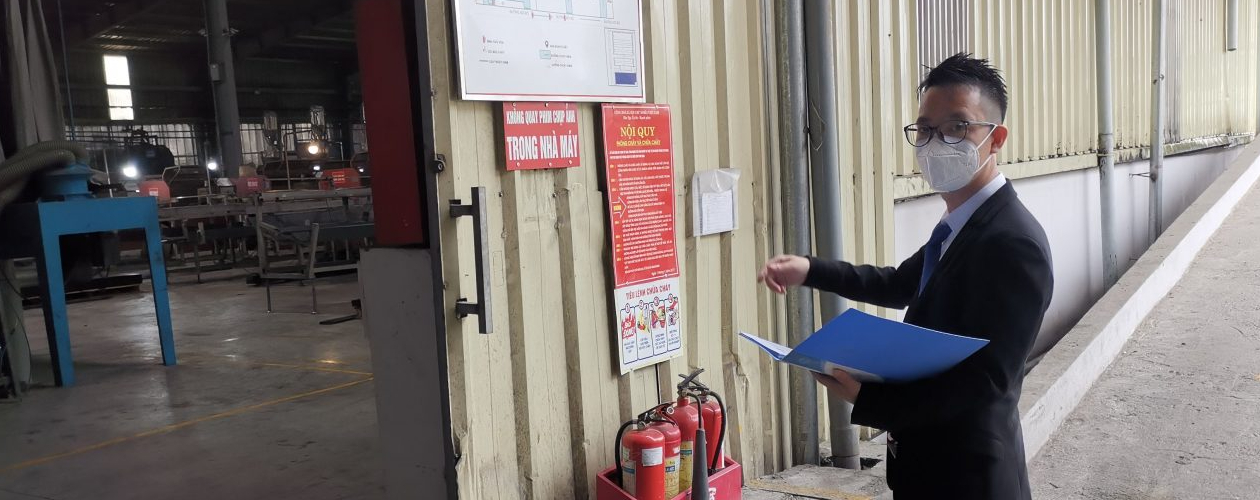
You might have heard of a factory audit if you’re sourcing products from overseas suppliers. But what exactly are they, and why are they essential for your business?
What is a Factory Audit?
A factory audit evaluates a supplier’s production facilities to verify their compliance with the buyer’s requirements. The auditor examines the supplier’s equipment, personnel, procedures, and environment. They ensure the supplier has the capacity and capability to deliver quality products and services according to the buyer’s specifications. A factory audit can be conducted as a final step in selecting a potential supplier or as a tool for monitoring an existing supplier’s performance.
What are the types of Factory Audits?
How to Conduct a Factory Audit
A factory audit is a way to check your supplier’s factory and see if they can meet your requirements and standards. To conduct a factory audit, the auditor will follow these steps:
• Follow a factory audit checklist or standard: they have a clear and detailed list or standard covering all the factory audit aspects. They can use an international standard (e.g., ISO 9001, SA8000, ISO 14001, C-TPAT) or a client-specific protocol. The client may have a rating system that helps you evaluate the factory’s performance and compliance.
• Inspect the factory premises, equipment, machinery, and workers. The auditor will visit the factory and see how it operates. They must check the factory’s layout, cleanliness, safety, maintenance, and capacity. They will check the equipment, machinery, and tools used to make the product and observe the workers’ skills, training, behaviour, and productivity.
• Review the factory’s quality management system, production records, test reports, certificates, and licenses: auditor will check the factory’s documents and records that show how they manage quality in their production process. The auditor will also review the factory’s quality manual, procedures, instructions, standards, and policies and then examine their production records, test reports, certificates, and licenses that prove their quality and compliance.
• Interview the factory management and team: auditor will talk to the factory’s management and team and ask them questions about their roles, responsibilities, processes, and practices. It’s vital to assess their knowledge, competence, communication, and cooperation and listen to their feedback, suggestions, and complaints.
• Observe the factory’s social compliance, environmental performance, and security measures: Check how it treats its workers and the environment. The auditor will check their environmental impact, pollution control, waste management, energy efficiency, and security measures against terrorism and smuggling.
Conclusion
A factory audit is a valuable tool to help you verify your supplier’s factory and ensure they meet your requirements and standards. If you need help conducting a factory audit, contact us today. We can help you conduct a factory audit that meets your needs and expectations. We offer high-quality service with fast turnaround time, detailed reports, a private online report system, and competitive prices.